The manufacture of composite and aluminum cabins
Sigma takes an integrated approach to manufacturing by producing a wide range of cabin components in-house, which allows us to maintain quality control from the initial stages of production through to the final assembly. This industrial approach ensures high-quality manufacturing standards and product reliability. Our cabins—known for their robustness, aesthetic appeal, and innovative features—are the result of our team’s vast experience, specialized production facilities, and meticulous, ongoing quality inspections.
Production starts in our sheet metal and mechanical workshops. Here, our highly skilled team works with various metals including steel, stainless steel, and aluminum. These metals are folded, bent, rolled, and machined with extreme precision, and each part undergoes individual inspection.
For more intricate carrier shapes, we employ composite materials. This involves combining materials like phenolic resins, polyester, or epoxy resins with reinforcing elements such as glass or carbon fibers to create highly durable components. We use thermoforming techniques to produce large components, some of which measure up to 3 meters by 2 meters. Our mastery over these diverse manufacturing processes has enabled us to create capsules for iconic observation wheels like the London Eye, the Las Vegas High Roller, and the world’s largest observation wheel, Aïn Dubaï.
Bodyshop
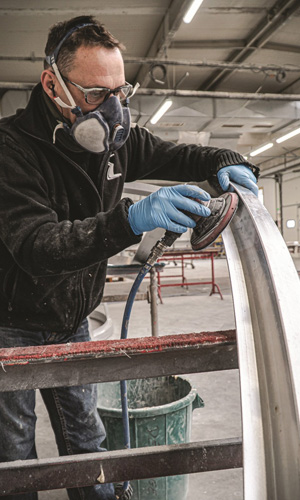
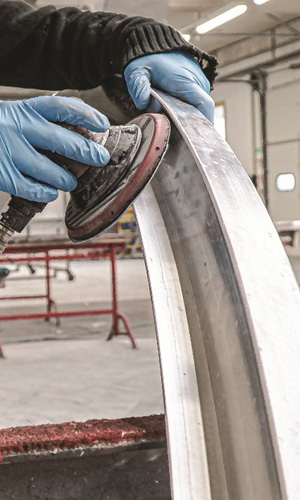
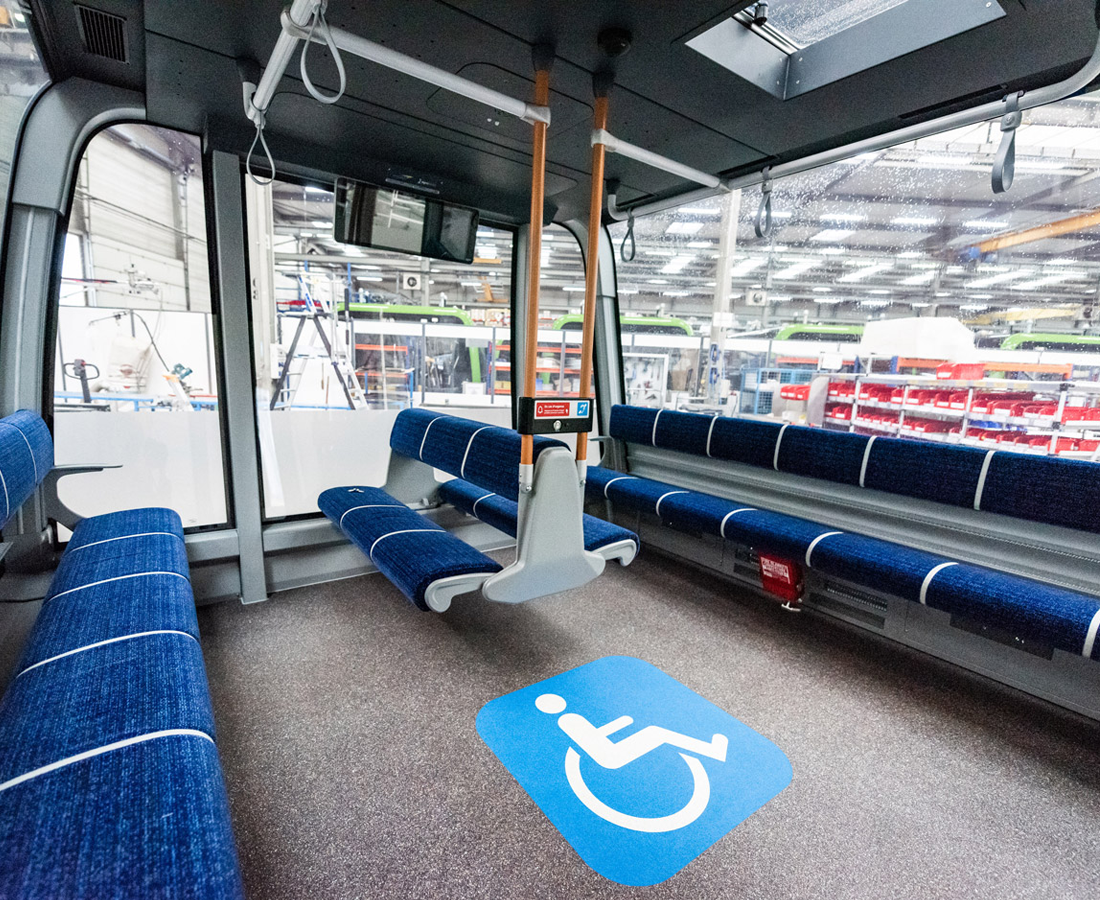
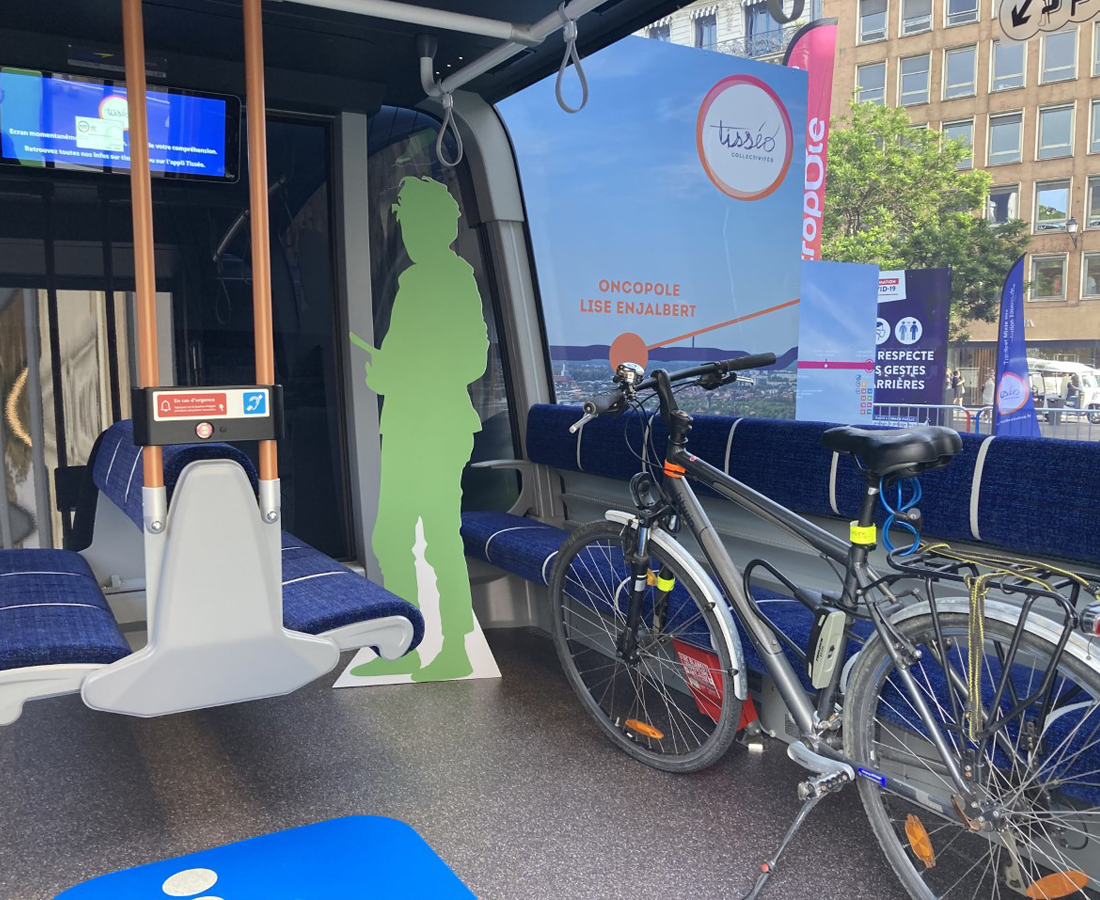
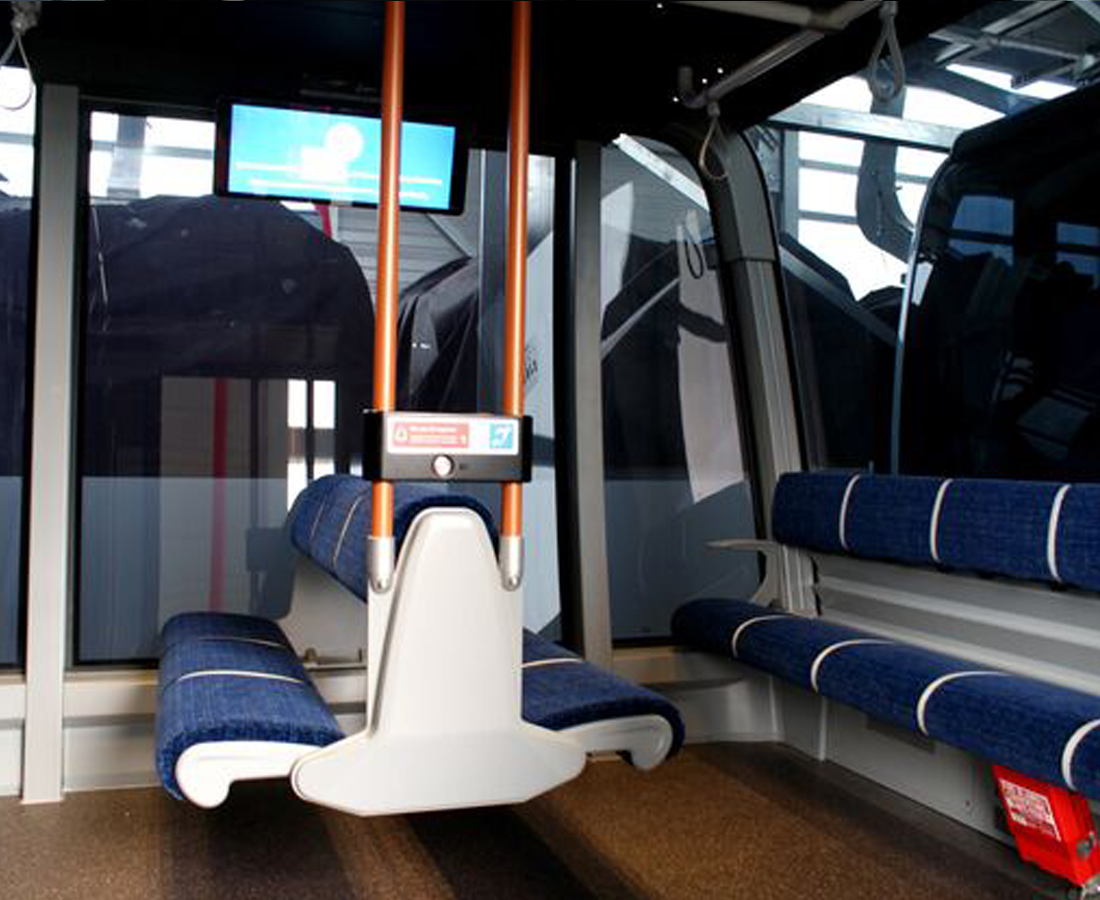
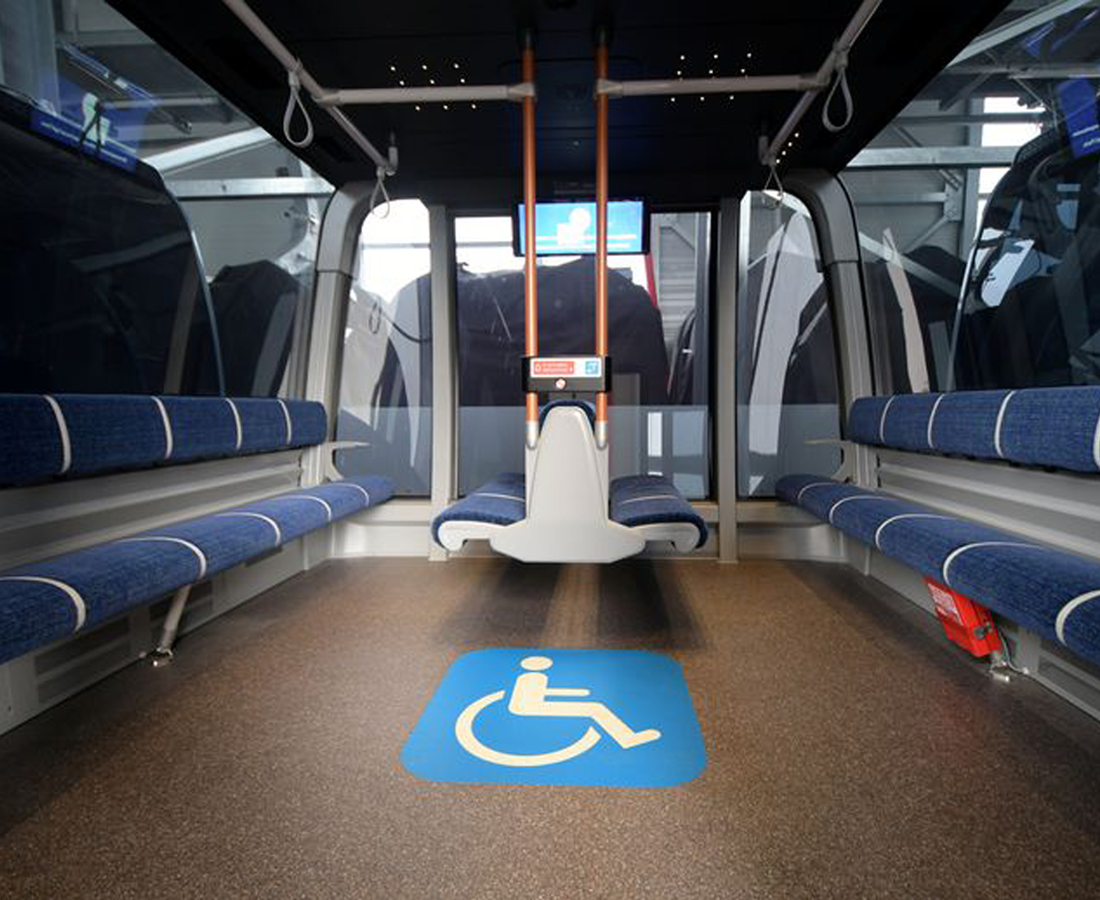
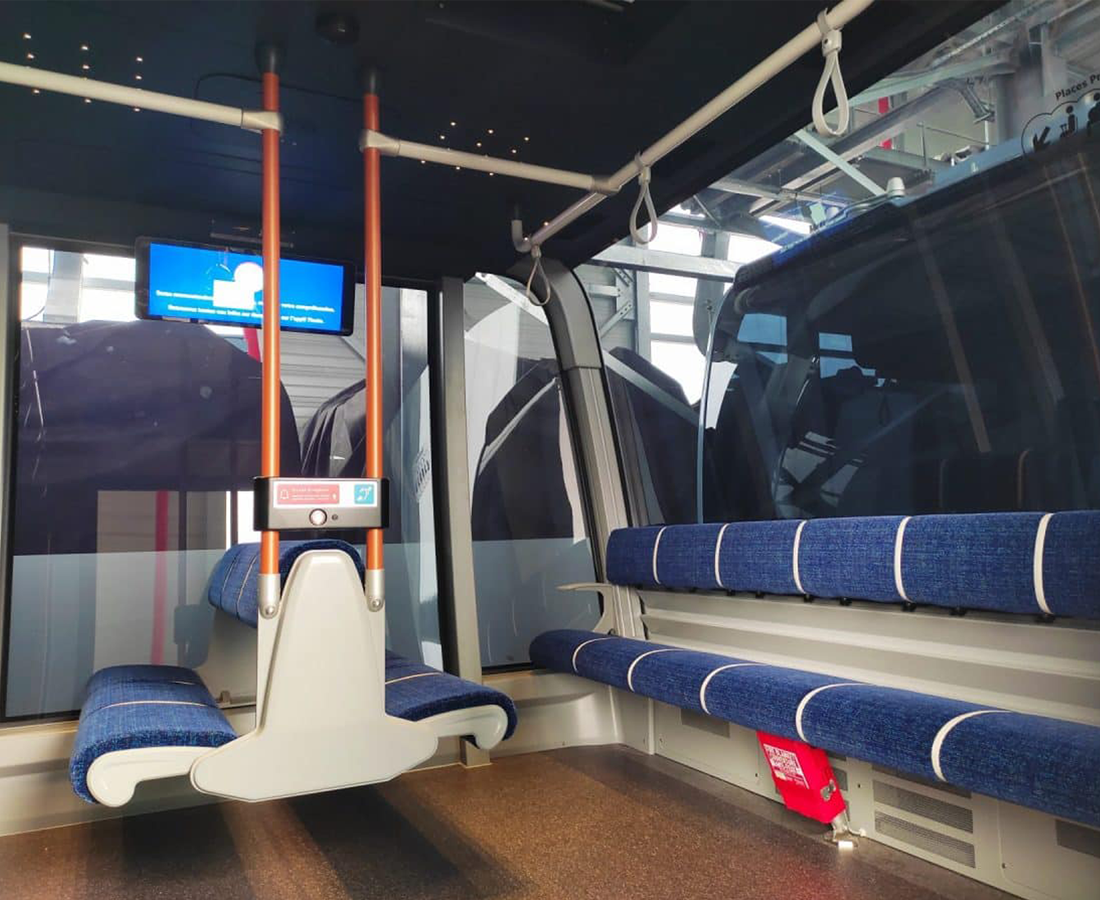
Carrier Personalization
Our expertise extends across various types of carriers: whether it’s cabins for gondolas and aerial tramways, trains for funiculars or APMs, or capsules for large observation wheels. This includes designing cabins that harmonize with their surroundings, high-capacity capsules featuring expansive panoramic windows outfitted with modern and elegant touches.
During the assembly stage in our workshop, carriers are tailored based on customer preferences. The customization options are vast—ranging from the installation of heated seats and accessibility features for those with mobility challenges, to mountain bike racks, air conditioning, onboard multimedia systems, and even solar panels for energy self-sufficiency. The end result is a perfect blend of our customers’ vision and our team’s ingenuity.
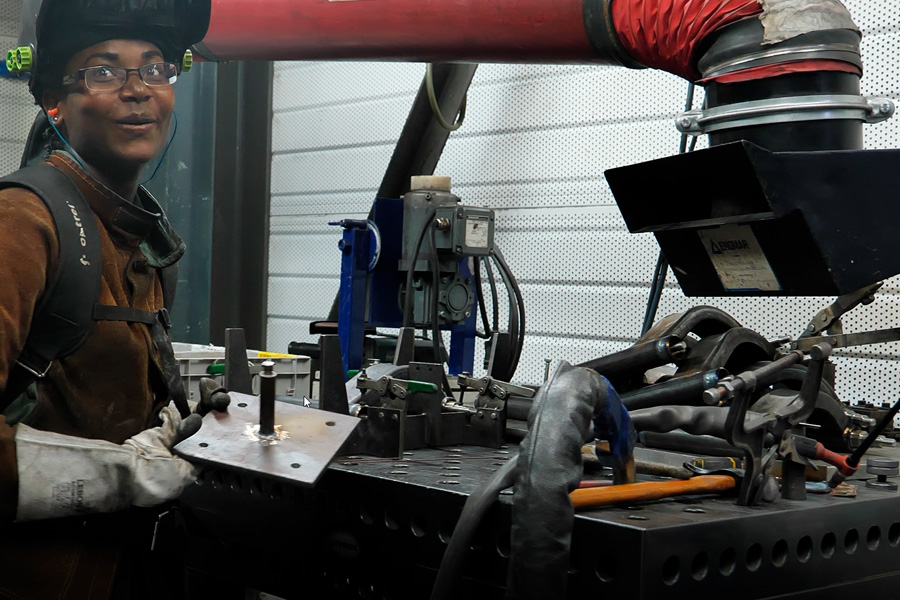
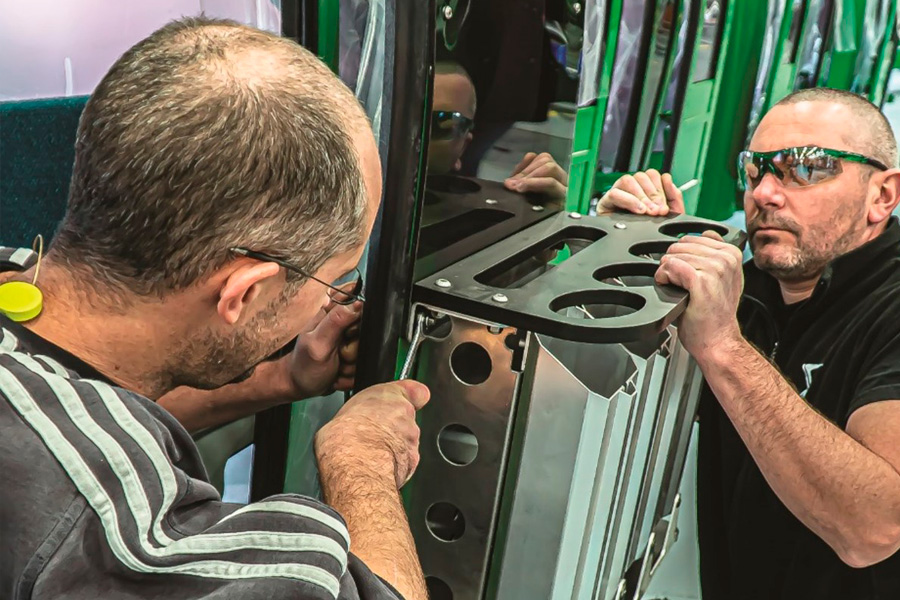
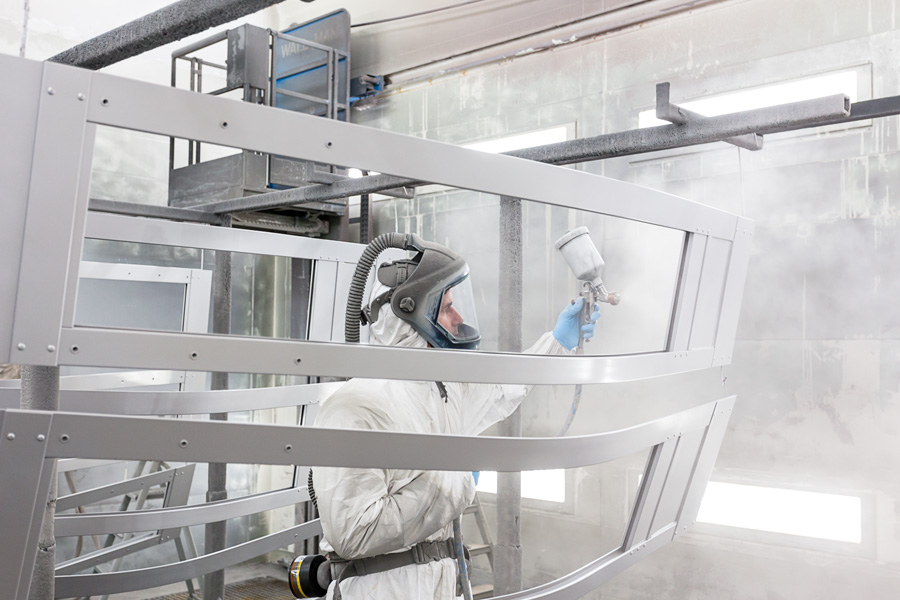
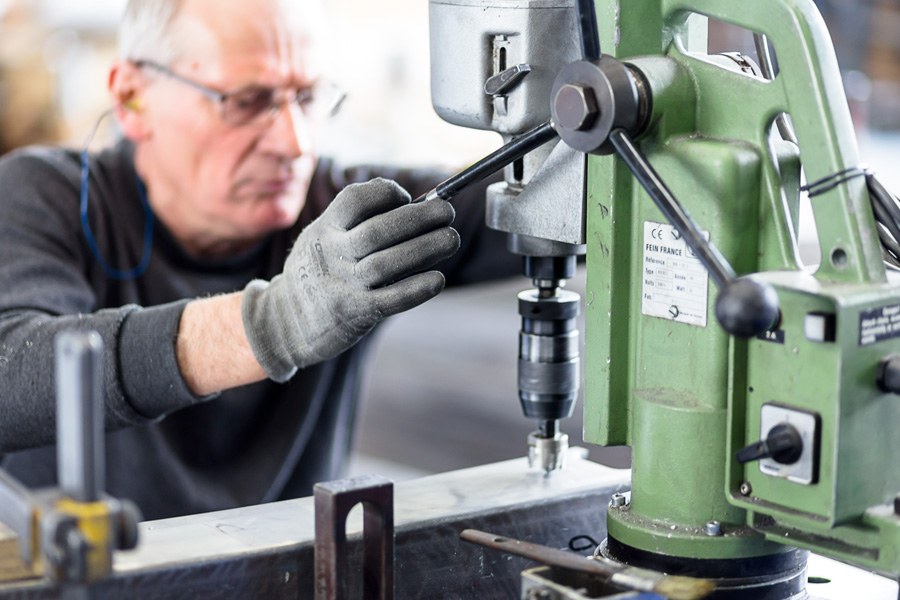
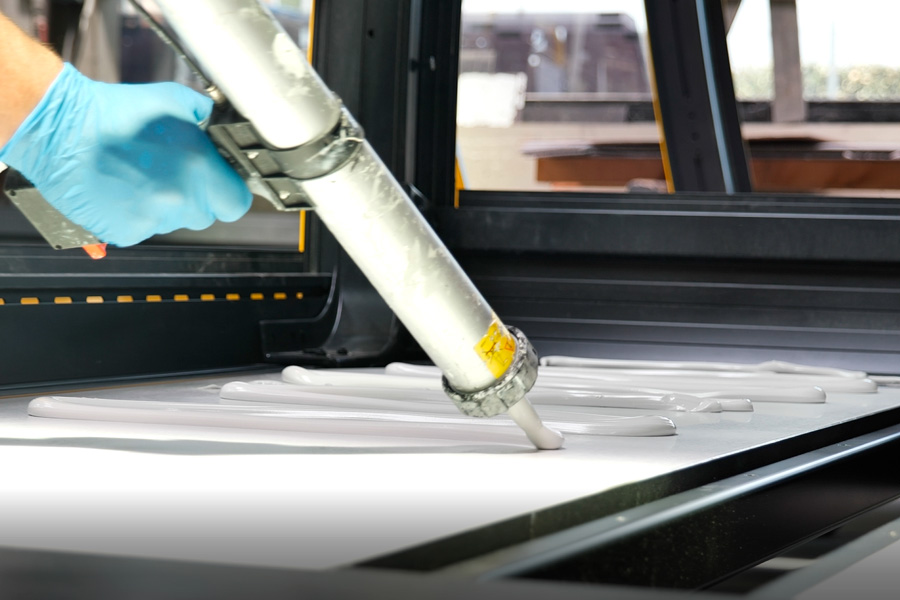
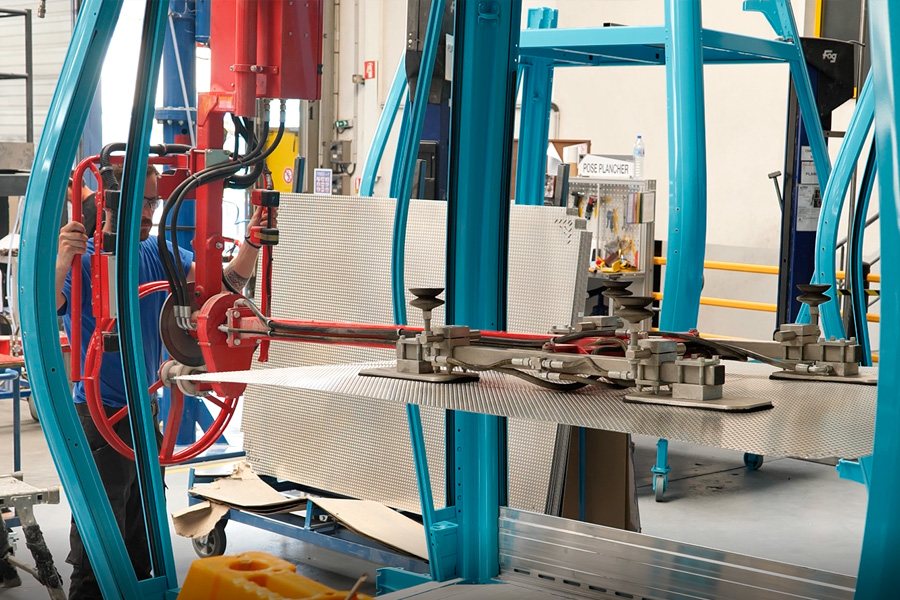
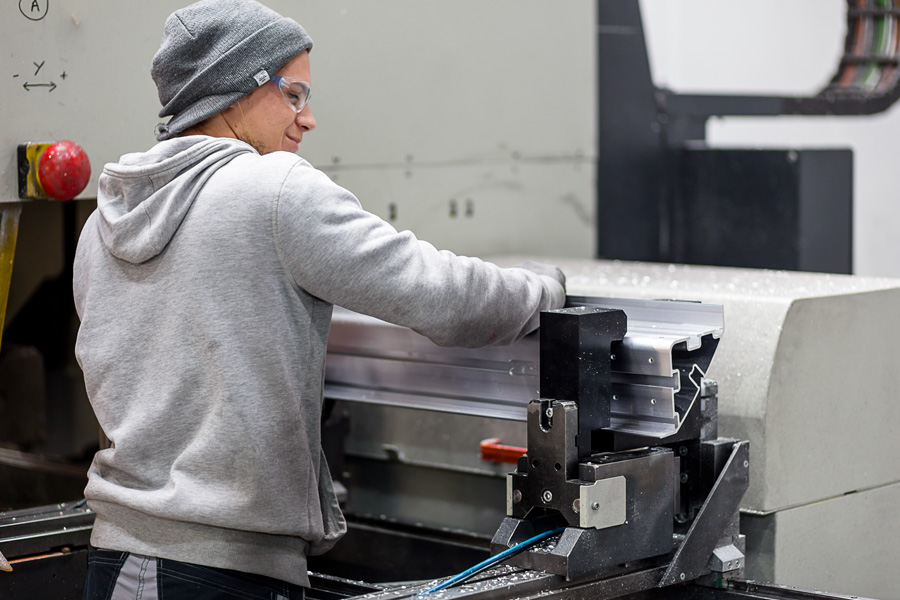
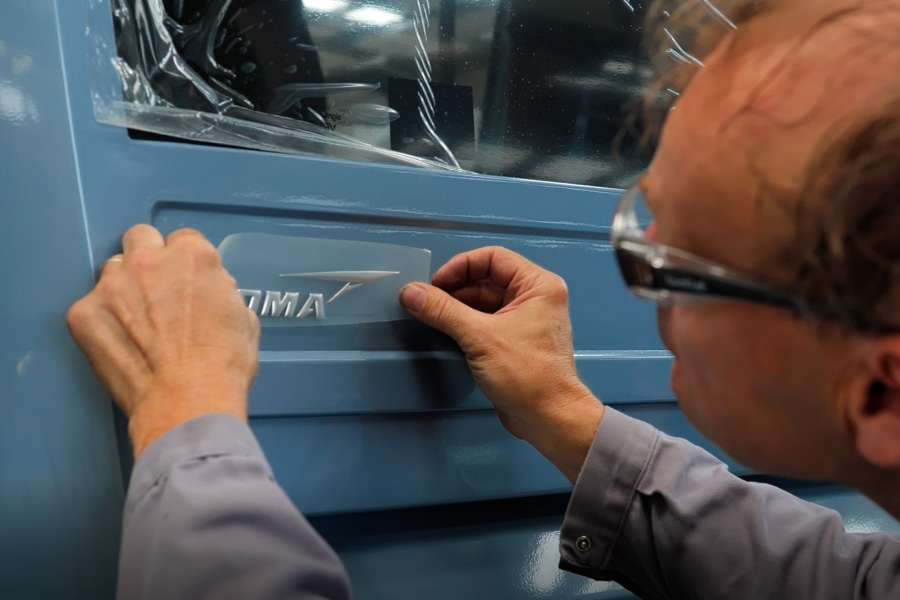
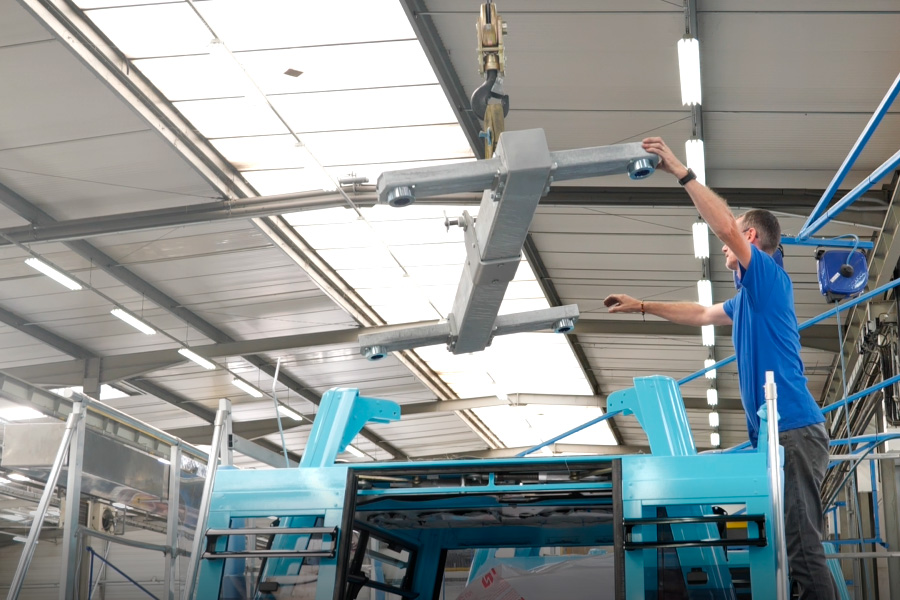
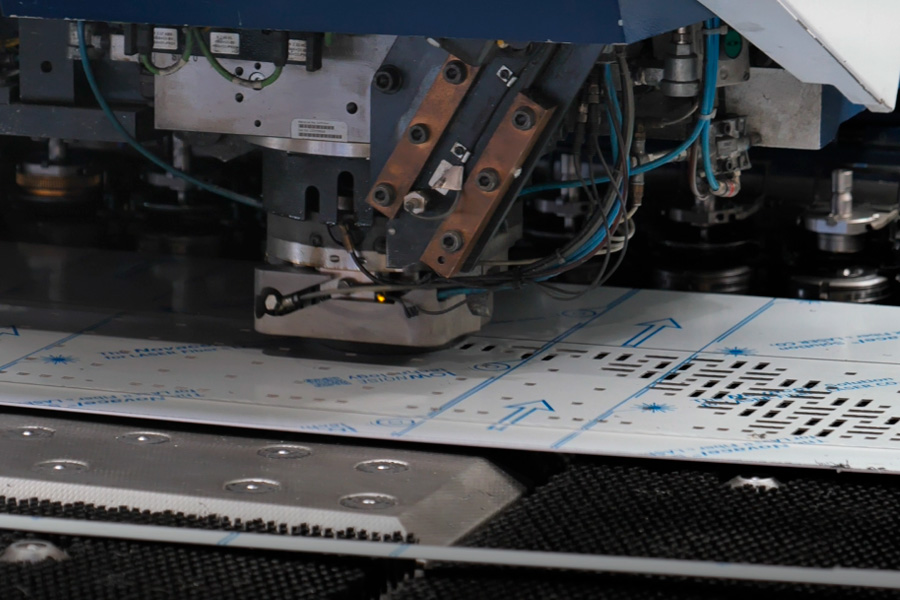
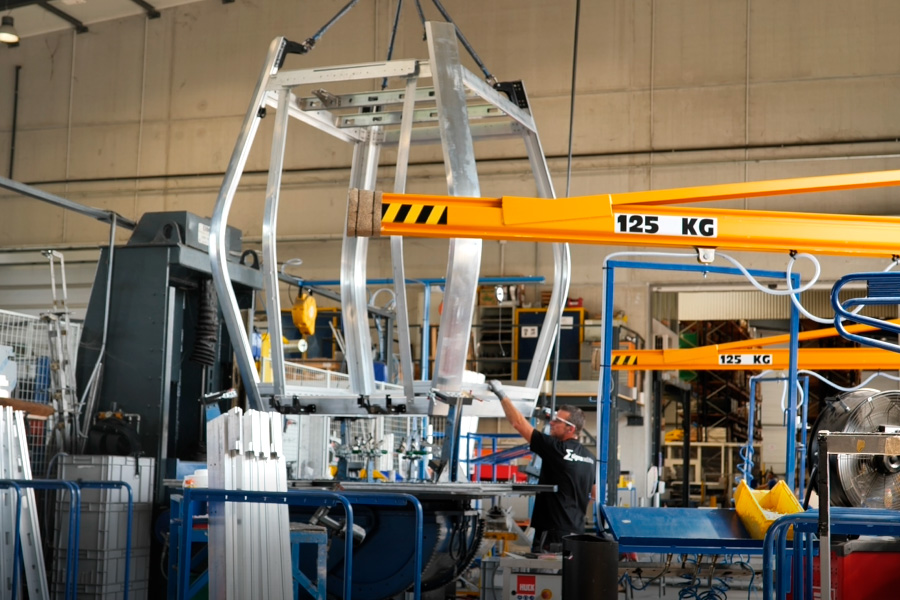
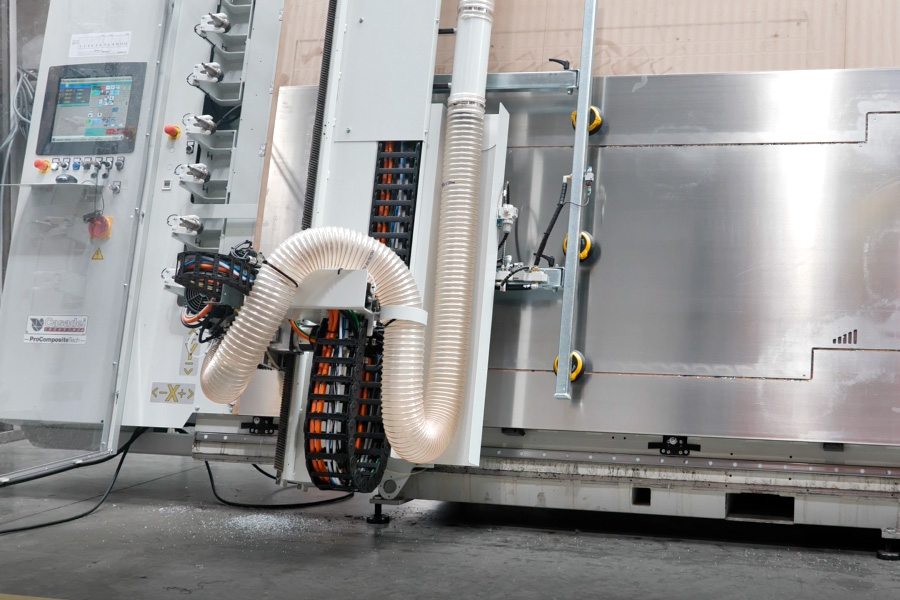
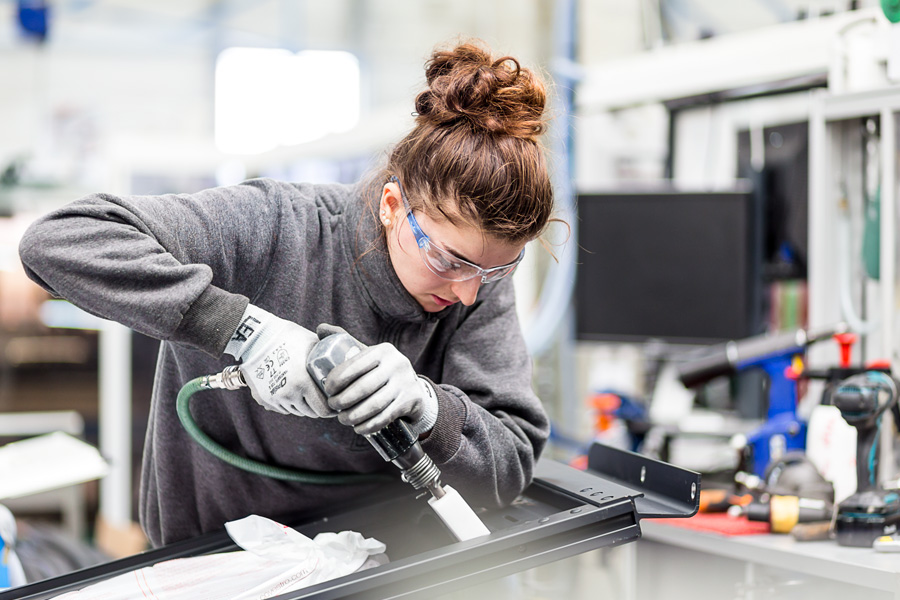
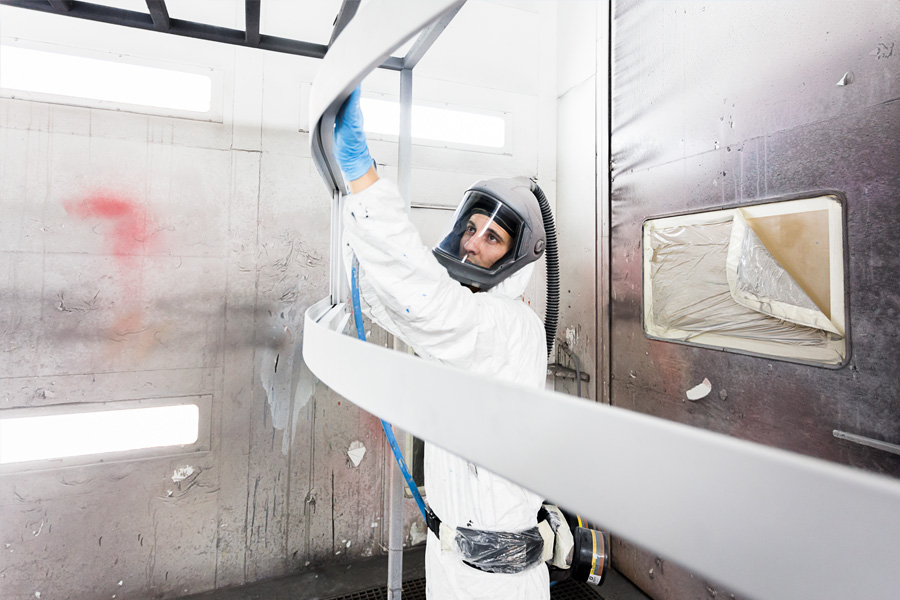
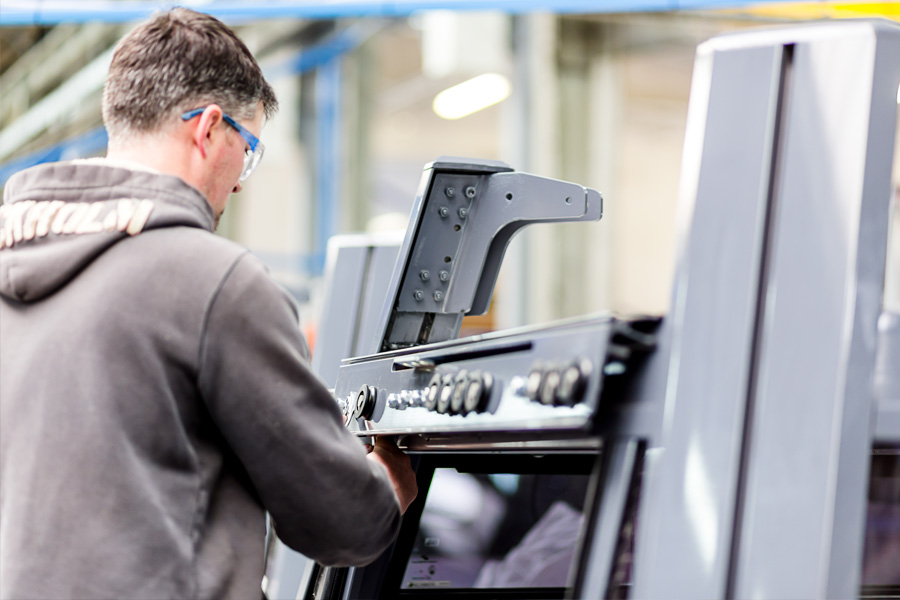
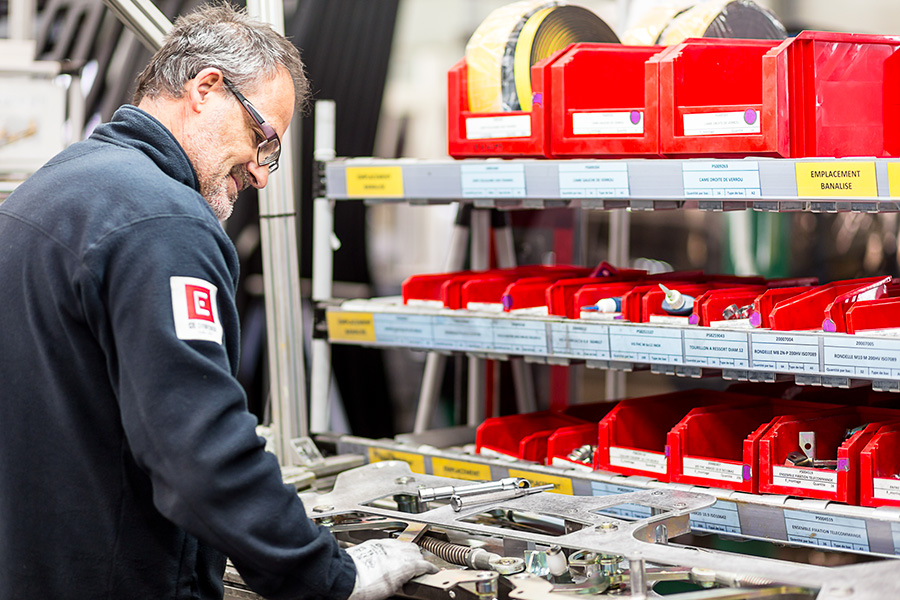